Briquetting, the processing of the material in pieces of geometrically regular and uniform in each case form, almost the same mass - briquettes (French briquette). When Briquetting create additional raw materials of fine materials (mainly fossil fuels and ores), whose use is inefficient or difficult, as well as recycled waste (dust, slag, metal shavings, etc.). Feasibility Briquetting in each case, the economically justified.
Depending on the source material is briquetting with binders (cement, glue) substances at medium pressures (10-50 Mn/m2) and without binders at high pressures (100-200 Mn/m2). For briquettes of high quality material, directed at pressing, must meet certain requirements (fractional composition, humidity, temperature, etc.).
Briquetting proposed in Russia in the 30-ies. 19. Russian inventor A.P. Veshnyakov, who developed a method for obtaining strong briquettes from waste wood and coal. 1859 in France SAHUT-CONREUR company in Raismes made first coal briquette factory, and in 1860 - with coal Roller presses. Agglomeration of fines briquetting widely used in the 2 nd half of 19.
The mechanism of the main stage Briquetting - pressing in general - is as follows. With a little pressure is external compression of the material through the voids between the particles. Then compressed and deformed the particles, among them there is a molecular clutch. High pressure at the end of compression leads to a transition of elastic deformation of particles in the plastic, resulting in the structure of hardened blocks and stored a given shape. The nature of the deformation is strongly influenced by physical and chemical properties of the source material.
Briquetting of fossil fuels (Dropped out of stone and similar old brown coal with a relatively strong mechanical structure, private’s weakly structured young brown coal and peat) is produced mainly for energy and public utilities in the briquette factories. Ash obtained briquettes to 20%. They are well oppose gravitational forces, withstand long storage in the open air, are not destroyed before the end of combustion. Briquetting is used as part of new methods of coking for metallurgical coke from the gas and weakly caking coal. Lean coal, anthracite, the old brown coal, semi-briquetted with binders (coal tar pitch in solid or molten liquid form, petroleum bitumen, etc.).
Fossil fuels with the use of tie briquetted scheme: receiving the source material (mixture of different coals), classification and grinding up to 6 mm or less, drying coal to a residual moisture of 3-4%, the binder preparation (crushing, melting), dosing and mixing of hot coal with a binder (6-10%) at a temperature of about 100 ° C to obtain a homogeneous mass (charge); cooling batch to 80-90 ° C, pressing at 15-30 Mn/m2 in Roller presses, briquettes cooling to 40 ° C. The most common form of briquettes, good tolerance to overload - ovate. Weight blocks 70-75, the major drawback of briquettes with pitch and petroleum bitumen binder, limiting their consumption - the allocation of soot and low thermal stability. Processing techniques are introduced such briquettes hot gases that contain a certain amount of oxygen, or solid coolant, this is accompanied by oxidative polymerization of the binder, resulting in briquettes hardening and burning burning smokeless flame. Finds the method of distributing the so-called. Hot Briquetting, allowing no tie to receive high-quality coke and smokeless fuels by pressing pre-heated to a plastic state caking coals or in a mixture with no caking coal (anthracite, lean and brown coal) and semi-coke. Young brown coal with high moisture content (from 45 to 60%), the pieces are in storage and transportation destroyed, briquetted without a tie (for bed firing): reception of coals, dosing, the classification of coal on disc or sieve screens and crushing it in hammer mill to the grain size of less than 6 mm , drying of coal in the steam tube dryers or gas pipe-dryer to an optimal moisture content 14-19% additional fragmentation of large particles of coal, coal cooling (in some cases does not apply), leaving the dryer with a temperature of 85 -- 90 ° C in the cooler to a temperature of 35-45 ° C, pressing at a pressure of 100-200 Mn/m2 tape stamp, at least - in the ring presses, cooling bricks, leaving the press with a temperature of 70-80 ° C, cooling trenches and mesh conveyors to a temperature of 40 ° C; shipping bricks to customers. Briquettes are in the shape of a parallelepiped with rounded corners. Weight briquette 500 - 600 g .
Milling peat with moisture content up to 25% in the floor briquetted pellets in ribbon stamp presses. For peat briquettes with high humidity (50%), it is dried to a moisture content 12% in an oven (air, steam, steam pipe, steam, air, gas), which mainly determine the pattern and Briquetting peat.
Briquetting peat with air and gas drying is carried out under the scheme: classification and segmentation (in some cases) of incoming raw materials to a size of less than 6 -10 mm ; drying flue gases in the air and gas dryer (tube-dryer, a dryer with a fan or shaft grinding mill) the capture of dry peat in the cyclone, pressed at a pressure of 7-20 Mn/m2 cooling of briquettes in cooling water trenches up to 40 ° C.
Development of briquetting of fuel is characterized by the development and implementation of new schemes and stages briquetting binders apparatus for obtaining high-quality smokeless fuel, and in relation to methods of continuous carbonization in order to expand resource base and improving the economy coking industry.
World production of coal briquettes is around 110 million tons per annum (incl. 85% brown coal) in Russia produced about 8 million tons of coal (70% brown coal) and about 7 million tons of peat briquettes per year.
When Briquetting ore source material is iron ore fines (separately and mixed with fuel), small and powdered ferrous metal, blast furnace flue dust and other metallurgical wastes. Binders are used: lime, various cements, silicates, etc. Briquetting is a Roller or stamp presses the scheme: dosing and mixing of ore with a binder, pressing the mixture sticks to the consolidation of their hardening (curing, roasting, steaming, drying). Iron ore pellets are sent to the open-hearth and blast furnaces, pellets of non-ferrous metals - in the reverberatory furnace.
Effectively briquetting metal chips and waste non-ferrous and ferrous metals. The direct use of this voluminous mass of loose metal presents a number of difficulties: rusting during storage, the inconvenience of transportation, fumes from smelting, etc. Briquetting chip eliminates these shortcomings and provides an opportunity to get out of it full metal. Briquetting implemented by compressing fine crushing, cleaned of impurities (oil, etc.) chips in the hydraulic and mechanical presses. Heating the material directly under the pressing in some cases improves the process of briquetting.
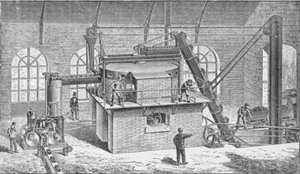
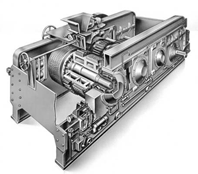
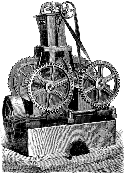
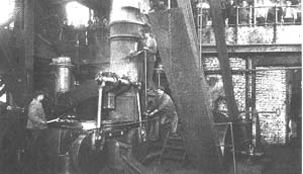